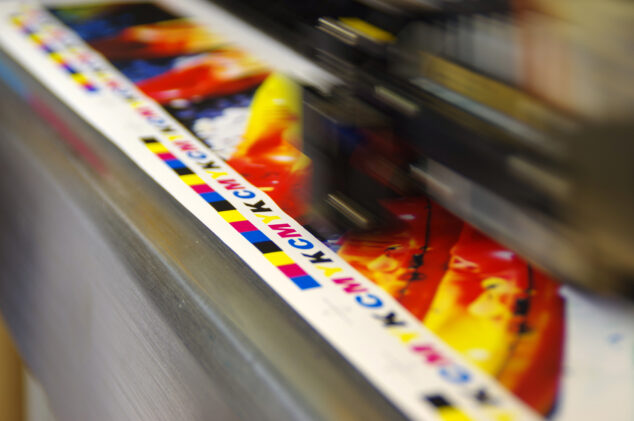
Complex technology requires clear terminology. ColorGATE CEO Thomas Kirschner explains why calibration and characterization must be distinguished in digital color management.
Characterization of the machine in the software
In the last article we have dealt with calibration. Or rather: with machine calibration. You may remember that we introduced the following differentiation:
- Calibration is mostly hardware-related and ensures the basic color differentiation capabilities of the printing press
- Characterization is used to match the settings of the data-providing software (RIP) to the properties of the calibrated press.
Between two worlds: the linearization in the software
What does this distinction mean for the linearization that you can create in the data-giving software? Linearization has a special role between calibration and characterization, because it stands between the worlds, so to speak: on the one hand, it is already located on the software end, on the other hand, it serves the same goals as the previous machine calibration – ensuring the printer’s color differentiation capabilities.
During linearization, a test form (also referred to as target) is printed and measured. It contains gradations of the primary colors. With this target, it is possible to determine the point at which no further increase in density can be observed for each color. This can be defined as the new one hundred percent ink application. An algorithm is used to calculate a correction curve that redistributes the ink application for the gradations of the primary colors so that a linear dot gain is guaranteed.
The conductor on stage: Matching software and hardware
To stay with the picture from the previous article: the press is now tuned and ready to “make music”. We can now move on to the characterization of the printing system. After we have made sure that the color differentiation capabilities of our printing system are generally ensured in the first step, it is now a matter of correctly matching the settings of our data-giving (RIP) software to the properties of the printer.
The characterization of the printing system is done by profiling, i.e. by creating an ICC profile. The term profiling is often confused with the calibration of a printing system. In fact, calibration is rather the prerequisite for creating a high-quality ICC profile – the more linear the output of a printing press is, the more accurately the ICC profile can give us information about its color space.
This is exactly what the ICC profile does: it enables us to make statements about the printer’s color space, e.g. about the deepest possible black, gray tones, light tones, saturated tones, etc. A profile is not a color correction, but a kind of lookup table that provides us with data pairs of Lab values and output color values of the printing press. It thus represents the actual color for each digital data combination. A print data generating software, e.g. the ColorGATE Productionserver, can use this look-up table to convert the color values from an input color space embedded in a file to the output color space of the printer.
It is important to note that this translation from an input color space to an output color space only works as long as all parameters and processes that influence the color remain unchanged. This is because a profile represents a combination of printing process, ink, media and other process parameters that can influence color. Depending on the industry, these can be, for example, firing curves of a kiln in the ceramic industry or dryer temperatures in textile printing. If these parameters change, theoretically a re-profiling is necessary to ensure that the software and hardware are again properly matched. Just as the machine calibration has to be carried out again if, for example, a print head has been replaced, the characterization of the system in the software also represents a momentary snapshot. Even if you do not make any conscious changes to the configuration of your printer, the character of the printing system will change over time, which can lead to color deviations.
One solution to avoid the all-too-frequent creation of color profiles is ColorGATE’s Media Device Synchronization (MDS), which allows you to define a reference state within the software. If you notice color deviations later on, you can use the MDS to calculate a correction, allowing you to effectively restore the reference state of the printer from the software end. This ensures that you can always reproduce identical results when printing on the same material.
0 Likes